Why Rogers High Fidelity®
I wanted to design and manufacture the highest quality audio amplifier using military, spacecraft and RCA design heritage and build it at a reasonable price. We are passionate about high power vacuum tube engineering and committed to producing a unique and highly sophisticated amplifier for the high-end audio consumer.
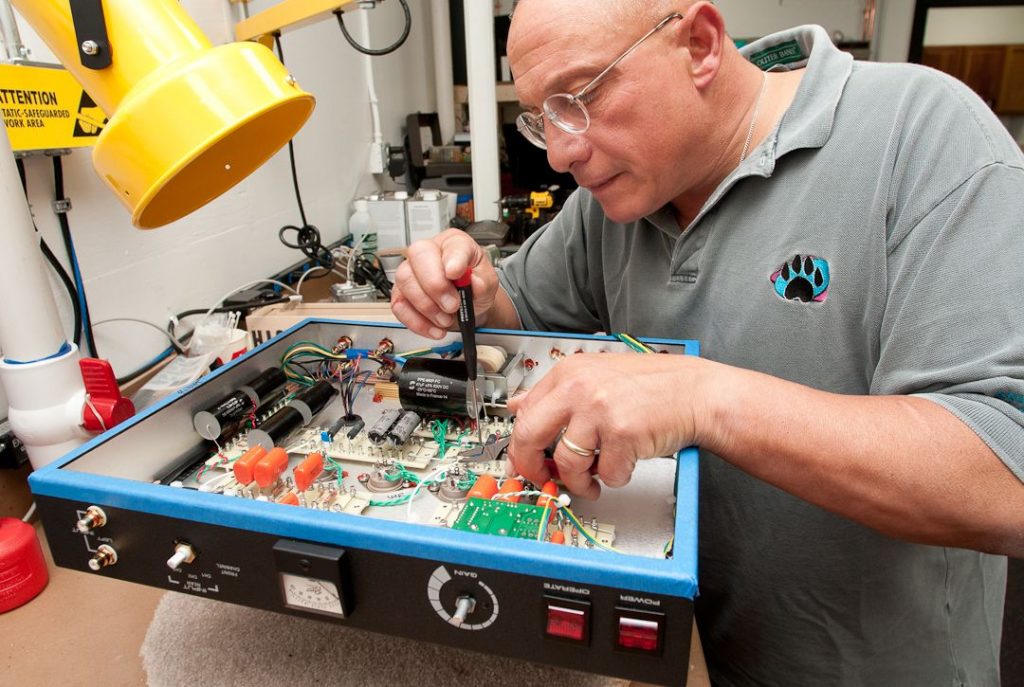
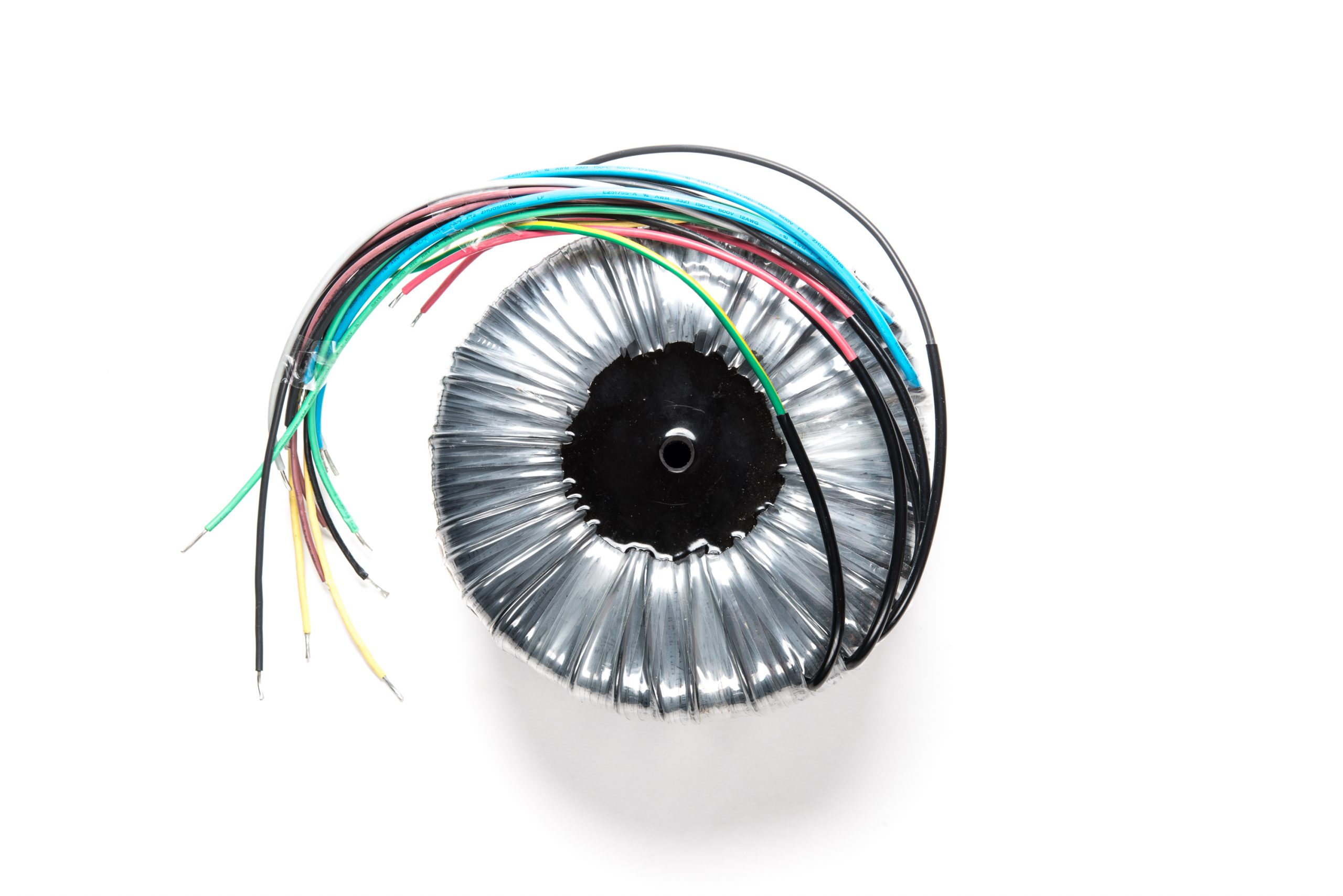
Lifetime Guarantee
I'm so sure of the quality and durability of my amplifiers, every unit is guaranteed for life. Not only that, but if you decide to upgrade to another Rogers model, the warranty of your old unit is transferable to the new owner. Our warranty is the platinum standard of the industry, and assures you that your purchase will provide lasting value – forever.
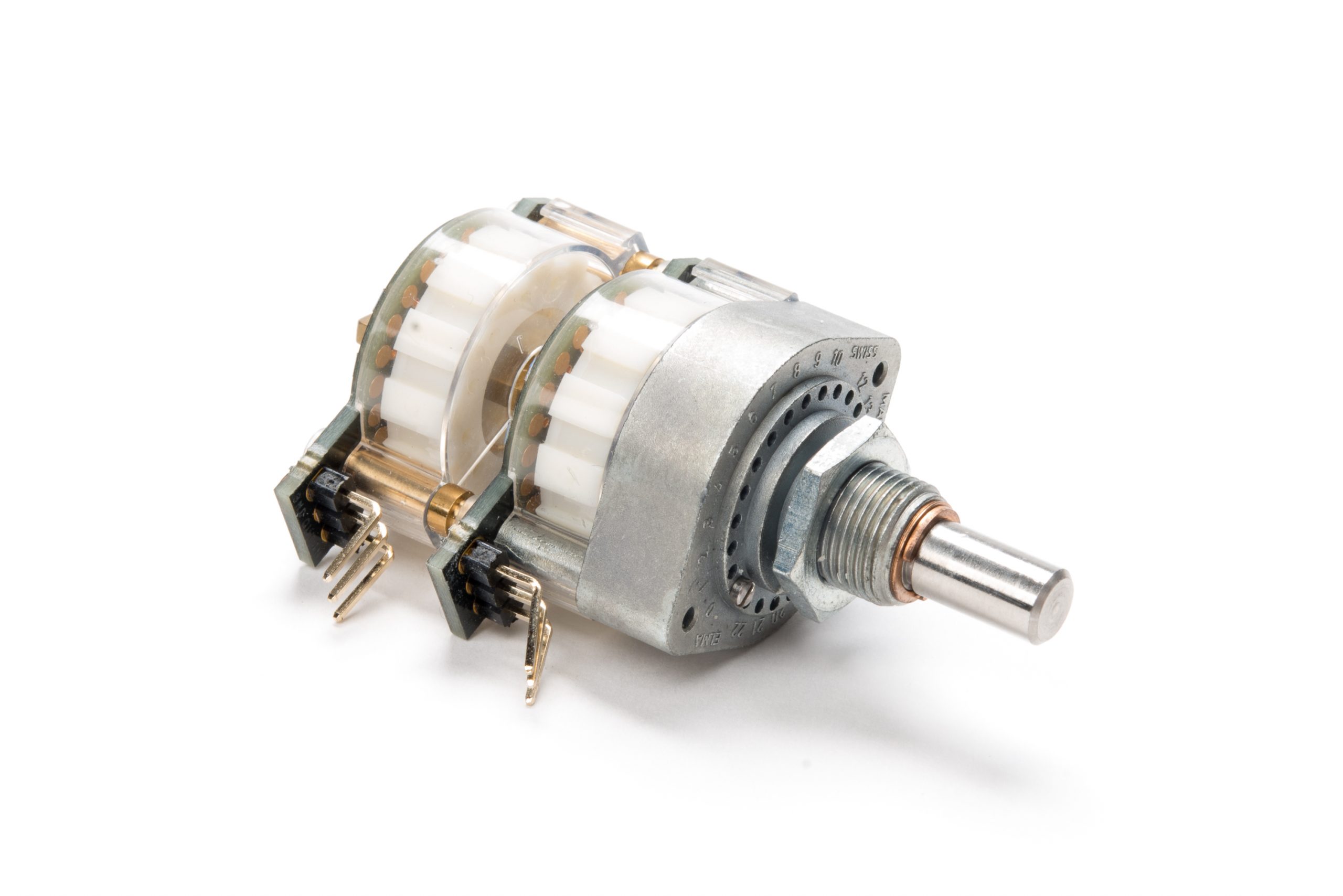
Aerospace Build Quality
Every unit is individually tested on Audio Precision test gear—the industry standard, and the best there is. Every single amplifier leaves our factory with a detailed test report, providing documentation of perfect performance, and detailing the fanatical lengths we go to in building our amplifiers.
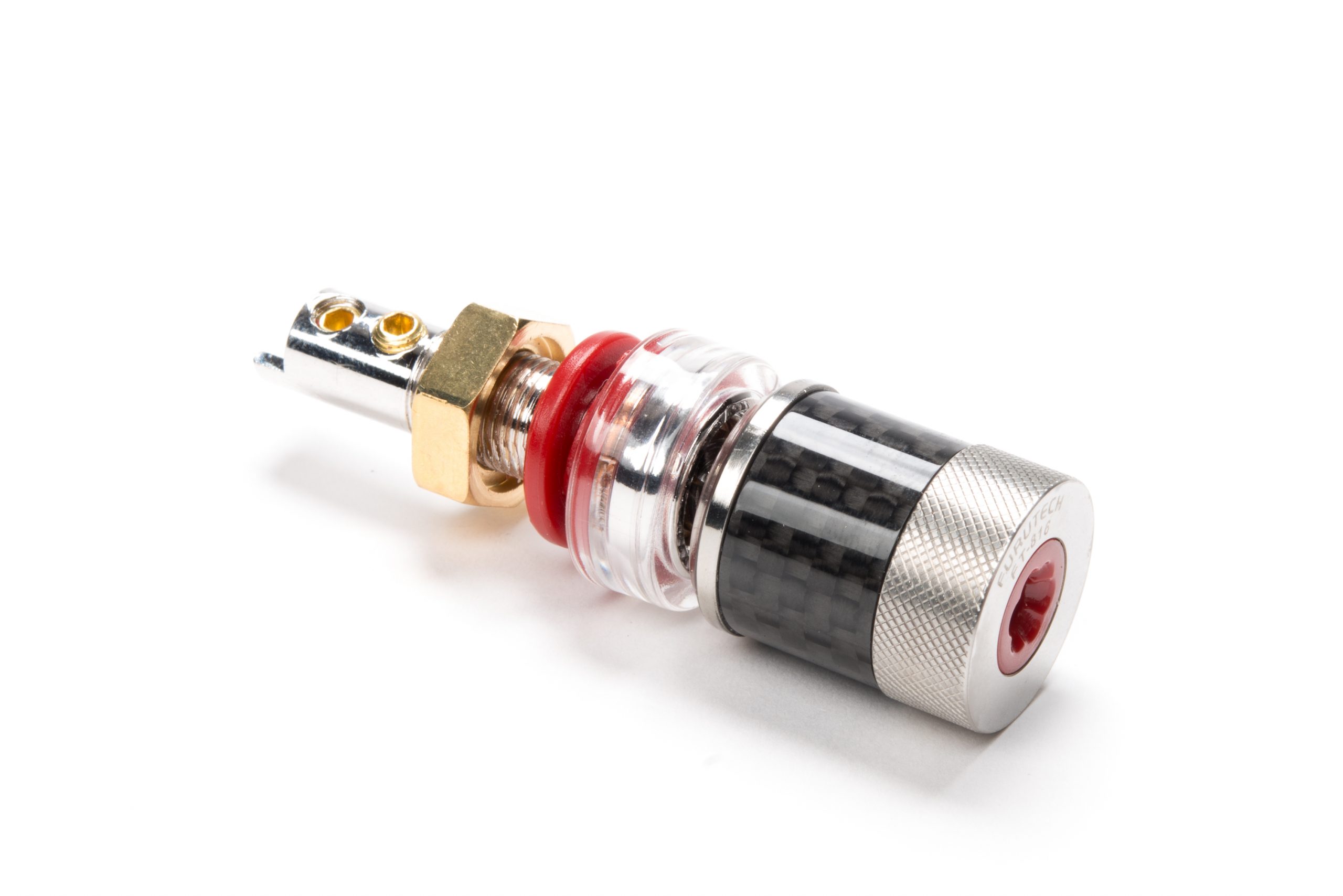
Made In The USA
My country means something to me so all Rogers High Fidelity® products are built by hand at my factory in Massachusetts. By employing technicians with years of experience working to the highest Military and Aerospace specifications, I can guarantee our products will provide decades of pleasure, trouble-free.
“We build each amplifier so your kids will fight over it when you’re gone.”
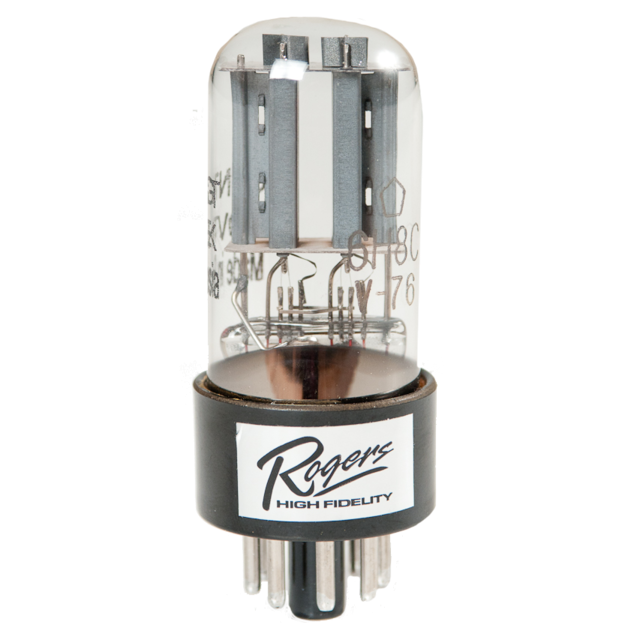
Tubes!
I build tube amplifiers on the grounds that the sound quality is more natural and satisfying than the sound from typical transistor amplifiers. Tube amplifiers have clipping and saturation characteristics that produce harmonic content differently than solid state devices making them sound richer and more natural (musical). Additionally, tubes are electric field devices rather than current devices and reproduce thermal noise in a truer fashion – this yields a more dynamic soundstage with richer detail and a more natural sound. Natural harmonic and noise reproduction make tube amplifiers a warmer more desirable amplification process.
How Our Amplifiers Are Built
In 1981, I began my career with RCA designing and manufacturing satellite ground terminals, Navy Aegis radar systems and the tracking suite for the NASA space station. It was at this time I learned how to manufacture equipment that could withstand the harshest of elements and still function perfectly. My passion for tube based electronics combined with my experience building virtually indestructible equipment (along with my love for music) has created the desire to create the finest amplifiers in the world.
Scroll to learn more.
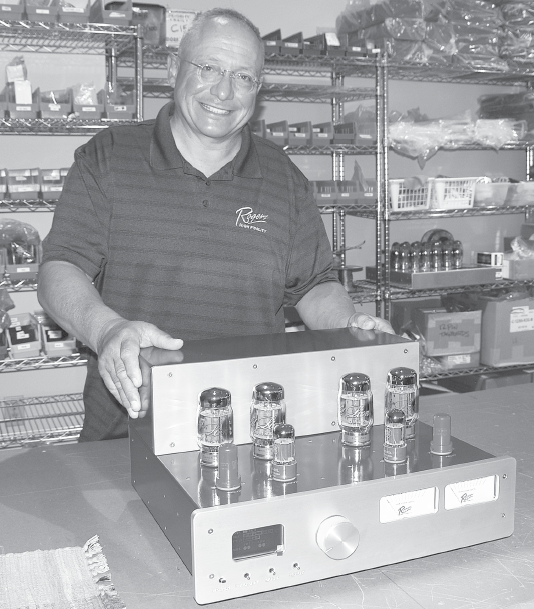
Our amplifiers are assembled and wired by hand at our factory in Massachusetts. Analog sections of our products utilize individual, discrete components—no chips!—and all wiring is point-to-point. These techniques are labor-intensive and far more costly than what you’ll find in throw-away electronics, but ensure a lifetime of reliable performance and serviceability.
Wiring and soldering of all Rogers products meet Military Standard 2000 requirements—sometimes called “Mil-Spec”. All our assembly technicians are trained and tested on these high standards.
Dual linear power supplies can easily handle large dynamic transitions in the audio signal, while maintaining a smooth and clear midrange. Vocals are presented with a truly rich and warm feel.
Wiring is the signal path of any amplifier, and it does make a difference in both durability and performance. We use 18 gauge Military Standard 16878 teflon coated, silver plated copper wire. This is expensive (besides being a mouthful!), but is used in mission-critical applications like the Navy’s AEGIS cruisers. Teflon coating provides heat-protection for decades, where common PVC-coated wire will crack and degrade over time. The 18 gauge wire provides greater signal capability than a trace on a printed circuit board, and ensures that the amplifier will be stable under any condition, and will never limit the dynamic range or transient abilities of your amp.
All our amplifier chassis are made from the same aluminum alloy certified for the construction of commercial and military aircraft. This ensures that each unit will be strong and vibration-resistant for its entire lifetime.
Each chassis receives a multiphase powdercoating, topped with a final clear-coat finish. The result is both beautiful, and bulletproof.
Front panels are machined from solid billets of aviation-grade aluminum, and each unit is assembled with Military Standard stainless steel hardware, with each fastener meticulously staked using an aerospace coating. We go to all this trouble to ensure ultimate reliability over a lifetime of use: the coating eliminates hardware failures caused by vibration, movement, or rough handling during shipping.
Every single resistor, capacitor, transformer, and inductor that goes into a Rogers High Fidelity amplifier meets or exceeds military quality standards for parts selection. This ensures that every unit will maintain the same performance documented on our test-bench, for decades to come. Our components are the same as those used by NASA in the Space Shuttle and the International Space Station, and by the US Navy in the AEGIS cruisers.
Power tubes are Russian, cryogenically aged and are 100% screened and tested prior to shipment.
Every single amp we build is “burned-in” at the factory for 100 hours before we even test it. That means it’s run at operating levels—not put in an oven! If resistors or capacitors fail, they generally do so in the first few dozen hours of use, and our 100 hour burn-in makes sure that all components have stabilized, and are ready for test. Following test, it’s ready for you.
Every unit is individually tested on Audio Precision test gear—the industry standard, and the best there is. Every single amplifier leaves our factory with a detailed test report, providing documentation of perfect performance, and detailing the fanatical lengths we go to in building our amplifiers.
We want every owner to be satisfied with their unit, from the moment it’s unboxed and plugged in – and for years to come.
All designs are environmentally tested in house:
- Cold soak 24 hours at -40 c
- Hot soak 24 hours at + 60 c
- Mil standard 1540
- 10 cycles from -40 c to +60 c
We protect our products even after they leave the factory. All our products are shipped in a custom-made double-box container system with die-cut high density and low density foam inserts. Our packaging is designed to withstand a 3 foot drop on any of its 6 sides, with no damage to the amplifier within. We have NEVER had an amplifier returned for shipping damage. NEVER.
My country means something to me so all Rogers High Fidelity products are built by hand at my factory in Massachusetts. By employing technicians with years of experience working to the highest Military and Aerospace specifications, I can guarantee our products will provide decades of pleasure, trouble-free.
I'm so sure of the quality and durability of my amplifiers, every unit is guaranteed for life. Not only that, but if you decide to upgrade to another Rogers model, the warranty of your old unit is transferable to the new owner. Our warranty is the platinum standard of the industry, and assures you that your purchase will provide lasting value – forever.
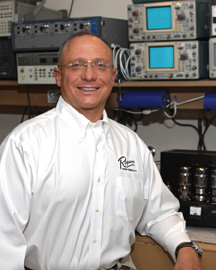
When You Buy My Amplifiers
You Get A Real Engineer
For more than 20 years I have led highly effective engineering and manufacturing teams that deliver results.
In 1981, I graduated from Drexel University with a BSEE and then in 1983, I was awarded an MSEE. For the next 3 years, I performed post graduate studies in electrical engineering, RF communications and antenna design. I also studied finance at the University of Pennsylvania Wharton School.
I devoted my professional career to designing and manufacturing high tech communications and radar equipment for the Department of Defense, NASA and several other agencies with demanding communications and engineering requirements.
I worked as an engineer for 13 years at RCA and General Electric. At RCA, I worked with some of the best radio design engineers in the world. At GE, I was part of the team that designed and produced the Communications and Tracking suite for the NASA Space Station.
I bring all of my quality, engineering and manufacturing expertise and experience to the home, high end audio market with my passion—Rogers High Fidelity®.
Rogers Newsletter
Sign up today and stay up to date on all of our latest offerings.
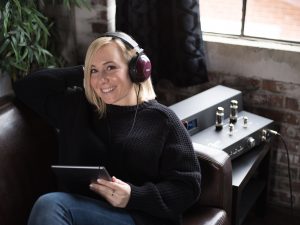